How identify Quality Grease Lubricant?
Find the ideal grease lubricants for your needs. Our products offer exceptional performance and protection, ensuring your machinery operates at its best.
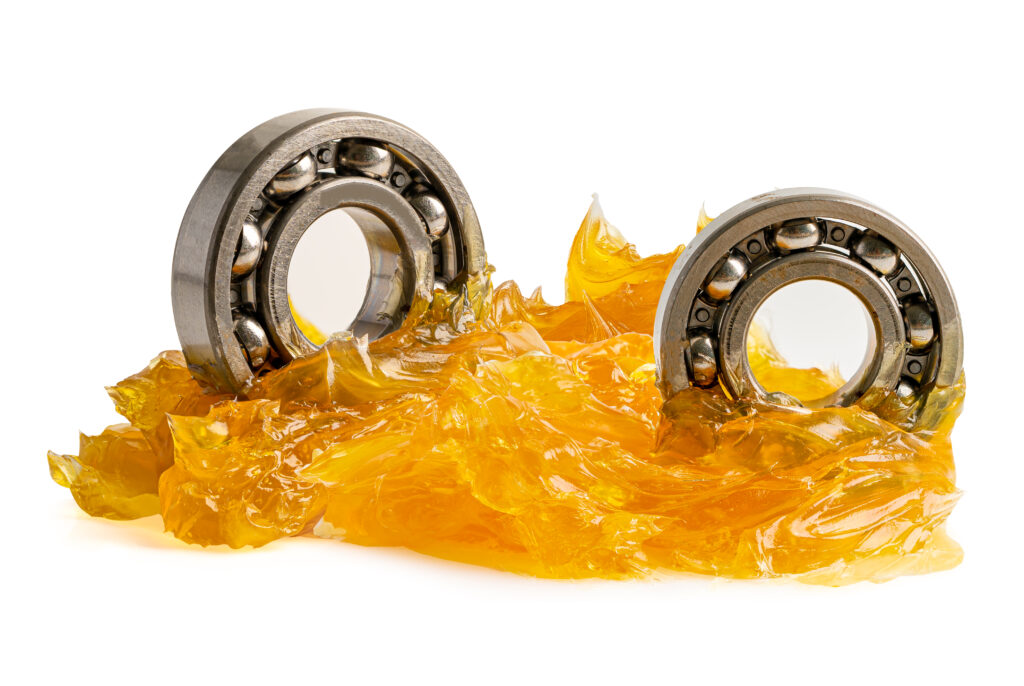
Definition of Grease:
Grease is a type of semi-solid lubricant made by combining mineral oil or synthetic oil with thickening agents, additives, and fillers. Grease lubrication can be more effective than oil lubrication in certain specific cases.
Properties of Grease:
The properties of grease depend on its composition and the nature of its components.
Viscosity of Oil: The viscosity of the oil used in grease is determined by the application temperature and the torque requirements of the machine. The grease should allow the machinery to start easily without excessive torque. For starting medium-torque machinery, the oil should have a maximum viscosity of 100,000 centistokes (Cst). Viscosity should be below or above 100,000 Cst for low or high-torque machinery, respectively.
Oils used in grease production typically have a viscosity of 200-500 SUS at 100°F. Maximum viscosity can be 3000 SUS, while minimum viscosity can be 100 SUS. Synthetic oils are more effective at both low and high temperatures, as their viscosity is less affected by temperature changes.
Loss on Evaporation: Loss on evaporation at high temperatures is an important property of greases and depends on the nature of the liquid phase. If a significant amount of oil evaporates, the grease’s lubrication properties are severely impaired, reducing its service life. Synthetic oils have lower evaporative losses than petroleum oils. The evaporative losses increase progressively from silicones, polyalkylene glycols, silicone-diesters, to high-temperature petroleum oils and diesters.
Oxidation Stability: Oxidation stability refers to the ability to resist oxidation. The oxidation stability of grease depends on the oxidation stability of the oil. If the oil is prone to oxidation
This creates acidity and a dark cream-like substance. As a result, the grease loses its lubricating ability. Since oil is a component of grease, oil oxidation occurs alongside grease oxidation. However, grease remains a safe lubricant up to a certain stage of oxidation. When the oil reaches its decomposition temperature, it turns into a solid, carbon-like substance, complicating the situation. Antioxidant oils or synthetic lubricants, such as silicones and fluorocarbons, have higher anti-oxidation properties and a longer lifespan than petroleum oils alone. Oxidation cannot be completely prevented, and eventually, the grease loses its effectiveness. The degree of oxidation increases with temperature, and there is a certain limit beyond which the grease can only be used for a short period.
Heat Stability: The gelling effect of the thickener
Grease contains oil, and different gelling agents have varying oil-holding capacities, which decrease with rising temperature. Some gelling agents can perform effectively at high temperatures, but none remain effective at the melting point or transition temperature. The melting point of grease is determined by a drop point test. The drop point is the temperature at which the grease becomes fluid enough to drip down from the bottom of a proof cup. This temperature marks the upper limit beyond which the grease is no longer solid.
In practice, the drop point does not reliably indicate the maximum usable temperature of the grease. The oil may separate from the grease before reaching the drop point, limiting its usability just below this point.
Heat stability, or thermal stability, is the temperature below the drop point at which the grease can retain its oil for a certain period. Lubricant strength is assessed by testing the amount of oil separation from the grease after exposure to a specified temperature. Grease with less oil loss due to separation is considered more stable.
Temperature Limits of Operation: The lower temperature limit for grease operation depends on the oil viscosity and the torque of the machine. At low temperatures, the oil viscosity should be low enough to allow easy machine startup. The lower temperature limit of the grease is determined by torque testing with a standard-sized bearing at a torque of 1000 g-cm. The upper temperature limit is determined by the grease’s heat stability and the evaporation loss or oxidation of its liquid phase. Grease can be used at any temperature for short periods, but it is not feasible to use it continuously at high temperatures or at any temperature over extended periods. Therefore, the maximum operating temperature of a grease is the temperature at which its degradation due to long-term use (1000 hours) — from evaporation loss or oxidation — remains within acceptable limits.
Consistency: Consistency refers to the density of grease, which depends on the density of the thickener and oil. It is expressed as the penetration value, which indicates the hardness and flexibility of the grease. The penetration value is defined as the depth (in tenths of a millimeter) to which a standard-sized cone (150 g mass) penetrates the grease under its own weight in 5 seconds at 25°C. This measurement is conducted using a penetrometer.
Characteristics of Various Soap Greases
Sodium Soap Grease: Sodium soap is used as a thickener with mineral oil. It is currently widely used in rolling element bearings because it is effective over a wide temperature range (from 30°C to 120°C). This type of grease is made of small fibers, making it suitable for low-speed bearings. It tends to absorb water, giving it great rust resistance; however, it is not water-resistant as it dissolves in water and forms an emulsion. Therefore, it can be washed off by water, making it unsuitable for applications where moisture is present. Sodium soap grease has a high drop point (usually not less than 180°C and in some cases up to 200°C), so it should be used at high temperatures.
Calcium Soap Grease: Also called cup grease, this type of grease is resistant to water. The soap grains used in this grease contain water, with a water content between 0.4-1%. At higher temperatures, the water slowly evaporates, weakening the soap structure. Therefore, this grease is typically used at low temperatures (around 60°C). Soap and oil may separate if used at temperatures above 60°C. In addition to water, stabilizers such as glycerol, glycol mono-oleate, propylene glycol, and wool grease are now used in the preparation of grease to enhance stability at higher temperatures.
Lithium Soap Grease: Lithium soap is used as a thickener, giving this grease a smooth or slightly grainy texture. It has a high drop point (around 190°C) and can be used at temperatures from 30°C to 150°C. This grease is water-resistant, mechanically strong, and compatible with various types of oils. Known as multipurpose grease, lithium soap grease is commonly used in bearings, chassis fittings, grease cups, universal joints, and water pumps. It is often made with lithium stearate soap, and, more recently, with soaps derived from hydrogenated castor oil to produce lithium hydroxy stearate grease. Lithium soap also serves as a base for synthetic greases.
Aluminum Soap Grease: In this type of grease, aluminum soap acts as a thickener, making it known as aluminum soap or aluminum base grease. It is transparent, smooth, and visually appealing, though it has a low drop point (90°C), poor mechanical strength, and becomes rubbery at high temperatures. Made from high-viscosity oil, aluminum soap grease is waterproof, non-sticky, and adhesive, making it suitable for chassis and gear lubrication.
Non-soap Grease Characteristics: Silica is a brittle substance commonly used as a lubricant. However, it can also be used as a gelling agent in colloidal form. Silica particles up to 50 microns are not abrasive, and the use of silica grease does not corrode parts more than ordinary grease.
Silica-based greases have good water resistance and can be used at high temperatures (up to 120°C). However, their mechanical strength is weak, and special care is required during manufacture. Greases prepared by mixing silica with synthetic fluids can be used at higher temperatures and inhibit oxidation. Due to their high cost, their use is limited to special cases or commercial applications. They are used as waterproofing grease in electrical apparatus.
For use in environments where inert gases are present, silica is combined with aromatic petroleum to create radiation-resistant grease.
Clay-based Grease: Finely divided clay particles of bentonite and hectorite are commonly used. Clay-based greases have high melting points, excellent water repellency, and can serve as multipurpose greases in industrial and automotive equipment. However, this grease cannot compete with lithium and sodium greases for use in high-speed ball and roller bearings. Organophilic clay grease has a special attraction for high-altitude applications.
Carbon Black Based Grease: This grease is not generally used. A special advantage of this grease is that it does not form objectionable deposits in high-temperature environments like other gelling agents. Both petroleum and synthetic greases can be made using carbon black as a gelling agent. Acetylene black is usually used in this application. Carbon black grease can be used up to 200°C.
Pure Petroleum Grease: A significant amount of asphalt type is sold as refinery bottom grease. According to the definition of grease, it cannot be called grease. A residual grease is highly viscous and has the same viscosity as lubricants used in heavy gear and rope lubrication, with graphite, mica, or fat sometimes added to achieve the properties required for specific applications. Its use is very limited because the melting point is low (115°F to 160°F).
Synthetic Grease: About 1% of the total grease used in the current market is synthetic grease. Among synthetic greases, diester grease is the most widely used. It is successfully used over a wide range of temperatures (about -55°C to 120°C). Polyester fluid is increasingly used because of its low evaporation loss.
Silicone greases can be used in a higher temperature range than organic esters. The evaporation loss of silicone grease is low even at very high temperatures (up to 150°C). Lithium soap is used as a thickener in this grease. Greases formulated with soap gelling agents can be used up to 170°C, while greases formulated with non-soap gelling agents can be used up to 230°C. Polyalkylene glycols and fluorocarbon greases are prepared for special applications. They are formulated with high melting point non-soap thickeners with alkyl biphenyl and polyphenyl ether oils for high temperature and radiation resistance.