How to Troubleshoot Reverse Power
Explore the concept of alternator reverse power and its implications for your electrical systems. Enhance your knowledge and improve your system’s efficiency today.
What is Reverse Power
Running an alternator or generator with power from the busbar or grid network is called reverse power. Normally, the alternator or generator produces electricity through magnetic flux and sends it to the common busbar or grid network. However, reverse power occurs when the power flows from the busbar or grid back to the alternator or generator motor.
Reasons for Reverse Power
Reverse power occurs mainly due to two reasons:
- Mechanical or prime mover issues
- Electrical or circuit breaker issues
a. Mechanical or Prime Mover Reverse Power
The prime mover’s job is to convert thermal energy into mechanical energy. In simple terms, it creates torque through the movement of the piston by igniting fuel, which gives rotational speed to the crankshaft. This rotational speed is transferred to the alternator coupled to the shaft, enabling it to produce electricity through magnetic flux. The prime mover essentially powers the alternator’s rotation.
However, If the prime mover is not able to produce that power, then the prime mover will not get its desired torque and the alternator’s rotational speed will decrease, resulting in the alternator not being able to maintain speed in line with the connected grid, meaning the power will flow in the opposite direction and the alternator will then consume electrical energy itself.
Reasons: If the effective pressure of the prime mover or engine decreases (e.g., due to reduced fuel in the combustion chamber), torque generation also decreases.
Solutions:
- Ensure proper fuel pressure in the engine.
- Adjust the governor’s common rack or control shaft to the correct position.
- Verify that the fuel rack or control shaft for each cylinder is in the correct position.
- Clean the fuel rack or control rod as necessary, using diesel to ensure smooth movement.
- Maintain the high-pressure pump and pipes in good condition to ensure fuel reaches the combustion chamber at the correct pressure.
b.Electrical or Circuit Breaker Reverse Power
Reverse power can also occur if:
- You signal the prime mover or engine to stop, or
- The engine control system signals the engine to stop due to a problem, but the circuit breaker fails to disconnect the alternator from the grid network or busbar.
Reasons:
- Issues in the signal communication of the circuit breaker.
- Malfunctioning of the open or trip circuit relay.
Solution:
Service the circuit breaker to ensure proper functioning.
Effect of Reverse Power
While reverse power does not cause immediate damage to the alternator, prolonged operation can have serious consequences:
- Other alternators or generators in the system may become overloaded.
- The alternator’s varistor and diode may burn out due to sudden voltage spikes.
- If the system uses a turbine, its rotational speed may increase excessively.
- The high-pressure pump in diesel engines, which relies on fuel for lubrication, may fail if emergency fuel is cut off during reverse power generation.
This happens because, during reverse power, the engine rotation is no longer driven by fuel combustion. Instead, it runs like a motor, taking power from the grid or busbar. Without fuel, the high-pressure pump loses lubrication and gets damaged.
How to work Reverse Power Relay
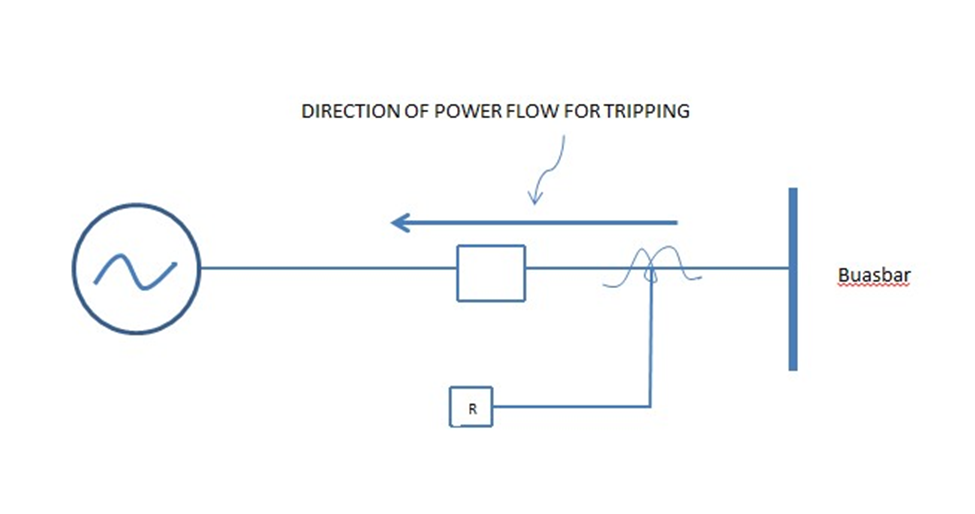
When the input to the turbine stops for some reason, the alternator starts drawing power from the busbar, i.e., it receives power in the reverse direction. To protect the system in such situations, reverse power relays are used.
In this system, a current transformer (CT) is connected either to the neutral end of the alternator winding or the busbar end.
When an alternator receives power in the reverse direction under abnormal conditions, the CT detects the current, which flows through the reverse power relay. This causes the relay to energize and trip the circuit breaker, thereby protecting the system. The reverse power relay measures both the value and direction of the power flow to ensure effective protection.
Function Reverse Power Relay
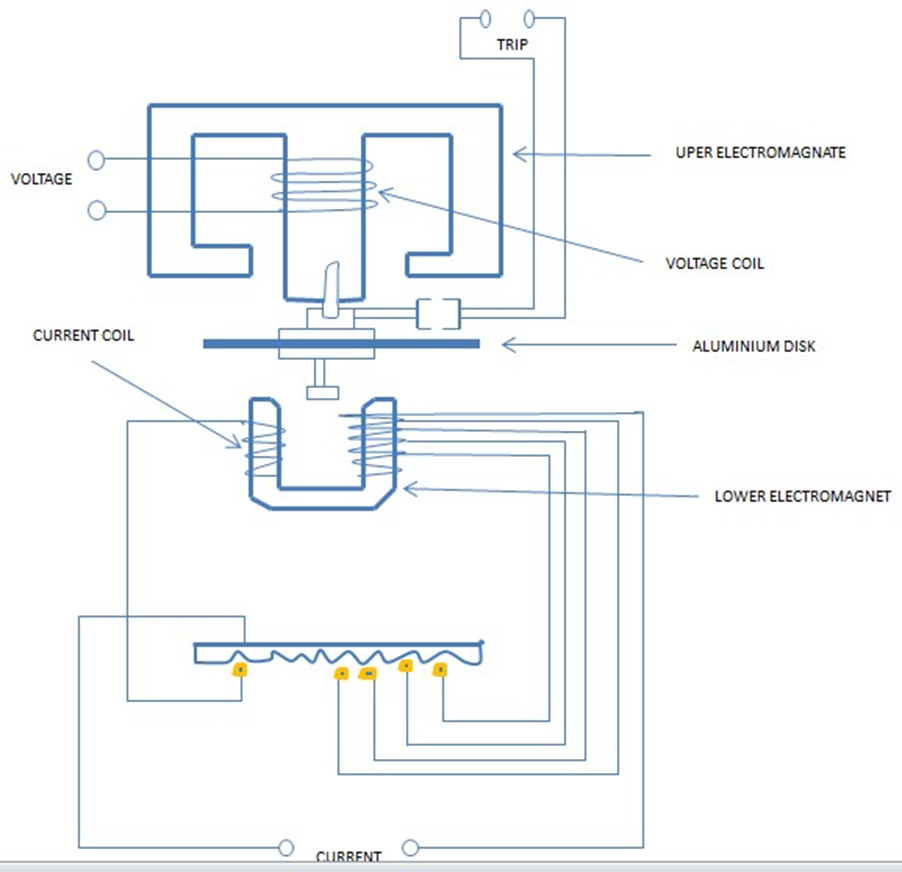
The construction of a reverse power relay is very similar to the internal structure of a wattmeter. Its design is almost identical to an overcurrent relay, except for differences in the windings and connections. It belongs to the induction-type relay category.
The construction and connection of a reverse power relay are shown in the accompanying figure. The relay consists of two electromagnets: one positioned above and the other below. The upper magnet has three arms, while the lower magnet has two arms.
A coil is attached to the inner arm of the upper magnet, and this coil is connected to the voltage source, typically through a potential transformer (PT). Another coil is attached to both arms of the lower magnet, which is connected to the current transformer (CT) through a plug-setting multiplier and is operated by the current.
An aluminum disc is mounted between the two magnets with the help of a pivot. A metal sheet is affixed to this disc, which completes the trip circuit when required.
In operation, a voltage-proportional current flows through the coil of the upper magnet, while a line-proportional current flows through the coil of the lower magnet. The interaction of these currents produces torque on the aluminum disc due to the flux generated by the two magnets. The direction of the disk’s rotation depends on the direction of the current flow. Under normal conditions, the interaction of the two fluxes causes the disc to rotate away from the trip coil contact, ensuring an uninterrupted supply. However, in abnormal conditions, when power flows into the system from the opposite direction due to a fault, the disc rotates in the opposite direction, moving towards the trip coil contact. This relay can be made more sensitive by using a sharper, more sensitive spring, which is alternately connected to the trip coil contact. This ensures the circuit breaker trips instantly and disconnects the circuit from the supply. The driving force in the relay is proportional to the power flow, making it highly responsive.
Such relays are typically used to protect synchronous machines or similar equipment from reverse current flow. However, they are impractical for use in short-circuit conditions.
Reverse power action refers to a protective mechanism in electrical systems that prevents damage by detecting and responding to unintended reverse power flow. This action is crucial for maintaining system stability and ensuring the safe operation of electrical equipment.